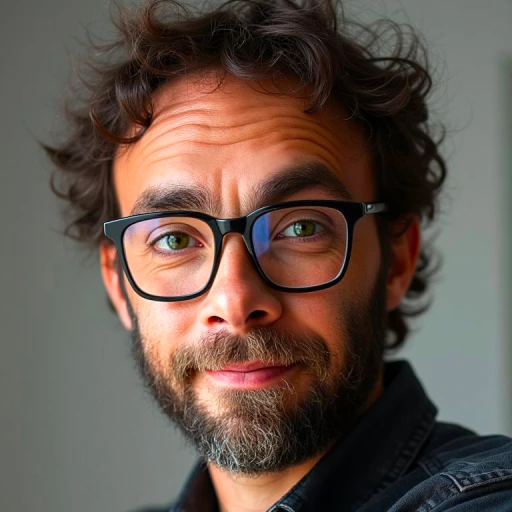
Comprendre l'analyse des causes racines
Qu'est-ce que l'analyse des causes racines ?
L'analyse des causes racines est une méthode systématique pour identifier la cause première des problèmes au sein d'une entreprise. L'objectif est de prévenir la récurrence des problèmes en trouvant et en corrigeant les causes profondes, plutôt que de se contenter de traiter les symptômes.
Par exemple, dans une étude menée par l'organisme ASQ (American Society for Quality), il a été démontré que l'application de l'analyse des causes racines pouvait réduire considérablement les coûts de non-qualité jusqu'à 50 %. Kaoru Ishikawa, souvent surnommé le père des diagrammes en arêtes de poisson, a souligné l'importance de cette méthodologie pour améliorer la qualité et l'efficacité des processus industriels.
Comment fonctionne l'analyse des causes racines ?
Le processus commence par la collecte d'informations sur le problème rencontré. L'étape suivante consiste à poser des questions précises pour identifier les possibles facteurs contribuant au problème. Par exemple, dans l'industrie automobile, Sakichi Toyoda a développé la méthode des « 5 Pourquoi », où l'on pose la question « pourquoi » cinq fois de suite pour atteindre la cause profonde d'un problème. Cela permet une identification efficace et précise de la cause racine.
Un article publié par International Journal of Lean Six Sigma révèle que 70 % des problèmes de qualité peuvent être résolus définitivement grâce à une analyse des causes racines rigoureuse et à l'application d'actions correctives appropriées.
Pour mieux comprendre l'intégration de cette méthode dans un système de gestion de la qualité, explorez la cartographie des risques mise en place dans certaines entreprises. Cette approche assure une qualité sans faille en sécurisant tous les processus industriels.
Les étapes clés de l'analyse des causes racines
Les phases essentielles dans le processus
L'analyse des causes racines, aussi appelée « root analysis » ou RCA, est un processus méthodologique visant à identifier les causes premières des problèmes pour mettre en place des solutions correctives efficaces. Voici un regard précis sur les étapes clés de ce modèle d'analyse :Définir clairement le problème
Pour commencer, il est crucial de bien définir le problème. Une définition claire permet de circonscrire les efforts de l'équipe autour d'un objectif commun. Par exemple, dans le secteur automobile, Toyota recommande de formuler les problèmes en termes de « faits observables » pour éviter toute ambiguïté. Un exemple célèbre de cette approche est le « Five Whys » de Sakichi Toyoda, qui consiste à poser la question « Pourquoi? » cinq fois pour remonter à la cause racine (https://www.cqo-at-work.com/blog/lanticipation-des-risques-fournisseurs-comment-piloter-avec-prevoyance-7-solutions-clairvoyantes).Rassembler les informations et les données pertinentes
Cette phase implique de collecter des données fiables et pertinentes pour mieux comprendre le contexte du problème. Kaoru Ishikawa, connu pour le « diagramme d'Ishikawa » ou « diagramme de la cause et de l'effet », prône l'utilisation d'outils d'analyse tels que les cartes de contrôle et les graphiques de Pareto. Ces outils aident à visualiser les causes potentielles des problèmes.Analyser les causes potentielles
Les diagrammes en arête de poisson (Ishikawa) permettent de décomposer le problème en ses différentes catégories de causes : matériaux, machines, méthode, main-d'œuvre, milieu, et mesures. Une étude de cas menée par l'Association pour l'Amélioration de la Qualité (AQR) en 2022 a démontré l'efficacité de cet outil dans la résolution de problèmes de qualité dans une entreprise de fabrication de composants électroniques.Identifier les causes racines
C'est ici que l'équipe doit se concentrer sur les causes premières. Le modèle « 5 Whys » de Toyota est très apprécié pour cette étape. Une enquête a révélé que 70% des entreprises qui utilisent cette méthode voient une amélioration notable de leurs processus qualité.Développer et implanter des solutions correctives
Une fois les causes racines identifiées, il est temps de développer des solutions. Par exemple, une entreprise de production alimentaire a mis en place un plan d'action correctif suite à une analyse des modes de défaillance et des effets (AMDE) qui a révélé des défauts dans la chaîne de distribution. En intégrant des correctifs, elle a réussi à réduire les réclamations clients de 25% en un an.Suivi et validation des actions
Enfin, le suivi est essentiel. Il s'agit de vérifier que les actions mises en place ont réellement résolu le problème sans provoquer de nouveaux dysfonctionnements. Une enquête réalisée par l'Institut de Gestion de la Qualité (IGQ) en 2021 révèle que le suivi rigoureux des actions correctives améliore la satisfaction client de 30%.Ces phases, lorsqu'elles sont bien exécutées, permettent aux entreprises d'améliorer continuellement leurs processus de gestion de la qualité. Pour des cas pratiques et des études approfondies, consultez notre section des études de cas de succès et échecs dans l'analyse des causes racines.Les outils d'analyse des causes racines
Les outils indispensables pour l'analyse des causes racines
Dans le domaine de la gestion de la qualité, l'outil choisi pour l'analyse des causes racines peut faire une énorme différence. Ces outils aident à identifier et à comprendre les causes profondes des problèmes de qualité, permettant ainsi de mettre en place des actions correctives efficaces. Examinons quelques outils essentiels pour cette tâche.
Le diagramme d'ishikawa ou diagramme en arête de poisson
Souvent appelé diagramme en arête de poisson en raison de sa forme, le diagramme d'Ishikawa permet de classer les causes potentielles d'un problème en catégories. Popularisé par Kaoru Ishikawa, cet outil aide à visualiser les relations entre les différents facteurs et effets liés à un problème spécifique.
- Utilisation : Le diagramme est particulièrement utile pour les équipes souhaitant explorer toutes les causes probables d'un problème avant de choisir celles à analyser en profondeur.
- Un exemple concret : Une usine automobile a utilisé cet outil pour identifier les causes d'une variation de qualité dans la production de pièces, permettant ainsi d'améliorer de 15% la qualité du produit final.
Les 5 pourquoi
Cette méthode développée par Sakichi Toyoda est essentielle pour creuser profondément les causes des problèmes. En posant la question "Pourquoi ?" cinq fois, il est possible d'atteindre la racine des causes sous-jacentes.
- Application pratique : Lorsque des défauts répétés ont été constatés sur une ligne de production de vêtements, l'équipe a utilisé la méthode des 5 pourquoi pour découvrir qu'un réglage incorrect de la machine en était la cause première.
- Citation célèbre : Toyota affirme que « poser cinq fois pourquoi » permet de ne pas se contenter des symptômes et de traiter les causes profondes.
Diagramme des modes de défaillance et de leurs effets (AMDE)
L'AMDE, ou analyse des modes de défaillance et de leurs effets, est une approche proactive pour identifier où et comment un produit ou un processus pourrait échouer. Cet outil évalue les impacts des défaillances potentielles et aide à planifier des actions préventives.
- Expert renommé : Par exemple, selon l'expert Jack R. Revelle, les entreprises qui intègrent l'AMDE dans leurs processus de conception voient une réduction de 50% de leurs défauts de production.
- Application dans les entreprises : Des géants de l'industrie comme Boeing utilisent l'AMDE pour garantir la fiabilité de leurs avions, contribuant ainsi à la sécurité aérienne mondiale.
Restons à jour : les outils modernes
Les outils d'analyse des causes racines ne cessent d'évoluer. Désormais, des logiciels spécialisés intègrent des algorithmes pour automatiser et affiner ces analyses. Par exemple, la méthode Lean Sigma combine plusieurs outils d'analyse pour optimiser les résultats et minimiser les défauts de production.
Les outils présentés ici sont essentiels pour une analyse approfondie des problèmes de qualité. Chaque outil a ses forces, et il est souvent utile de les combiner pour obtenir une perspective complète. N'oubliez jamais que l'efficacité de ces outils repose sur la rigueur et la collaboration des membres de l'équipe.
Études de cas : succès et échecs
Succès et échecs de l'analyse des causes racines
L'analyse des causes racines (RCA) est une méthode puissante utilisée dans la gestion de la qualité pour identifier les problèmes sous-jacents. Cependant, comme toute méthode, elle peut connaître des succès spectaculaires, mais aussi des échecs notables. Examinons quelques études de cas significatives pour comprendre les contextes dans lesquels la RCA peut soit réussir, soit échouer.
Des exemples de réussites à travers les industries
Les entreprises comme Toyota et General Electric (GE) sont des exemples emblématiques d'une application réussie de l'analyse des causes racines. Chez Toyota, le fondateur Sakichi Toyoda a popularisé la méthode des "5 pourquoi", une technique simples mais efficaces permettant d'approfondir chaque question jusqu'à l'origine du problème. Cette technique a largement contribué à la réputation de Toyota en termes de qualité et d'efficience.
De la même manière, GE a employé l'analyse des causes racines dans son programme Six Sigma, réussissant à économiser des milliards de dollars. Jack Welch, l'ancien CEO de GE, a admis que sans RCA, les améliorations continues réalisées au sein de l'entreprise n'auraient pas été possibles.
Quelques échecs notables
À l'inverse, plusieurs entreprises ont éprouvé des difficultés lors de la mise en œuvre de l’analyse des causes racines, essentiellement en raison de mauvaises pratiques ou d’une mauvaise compréhension de la méthode. Par exemple, une grande entreprise pharmaceutique a commis l'erreur de n'impliquer que la direction dans son processus de RCA, excluant les membres de l'équipe sur le terrain, ce qui a conduit à des résolutions de problèmes inefficaces et des solutions irréalistes.
De plus, certaines entreprises comme Boeing ont éprouvé des difficultés avec des analyses RCA superficielles ou incomplètes. Dans des cas comme ceux-ci, les causes profondes n'ont pas été correctement identifiées, ce qui a entraîné la répétition des mêmes problèmes.
Leçons apprises pour les entreprises
Les succès et les échecs de l'analyse des causes racines dans diverses industries montrent que l'implication de toute l'équipe et une compréhension approfondie de la méthode sont essentielles pour garantir des solutions efficaces et durables. Un exemple poignant est celui de l’importance de l’assurance qualité dans l’industrie pharmaceutique. L'implication des employés de tous niveaux hiérarchiques, et non seulement des décideurs, et une prise en compte sérieuse des causes premières sont des points clés pour éviter les échecs en RCA.
Les défis de l'analyse des causes racines
Manque de formation et de compétences
Les compétences de l'équipe peuvent sérieusement affecter l'efficacité de l' analyse des causes racines. Si les membres de l'équipe manquent de formation adéquate, ils risquent de passer à côté des racines des problèmes. Selon une étude conduite par l'Organisation Internationale de la Normalisation, 60 % des erreurs dans les processus industriels peuvent être attribuées à un déficit de compétences des travailleurs.
Résistance au changement
Les améliorations issues de l'analyse des causes racines peuvent provoquer une résistance au sein des équipes. Une enquête menée par le cabinet PwC révèle que 70 % des employés résistent au changement, surtout lorsqu'ils ne comprennent pas la nécessité ou les bénéfices escomptés. Pour contrer cela, il est crucial de mener une communication claire et de fournir des arguments convaincants sur les avantages potentiels.
Manque de données fiables
Une analyse des causes racines efficace repose sur des données fiables. Cependant, dans certains cas, les entreprises possèdent des systèmes de données obsolètes ou inefficaces. Selon une recherche de Gartner, près de 30 % des données recueillies dans l'industrie manufacturière sont jugées inexactes ou imprécises, ce qui entrave sérieusement le processus d'analyse.
Cas d'utilisation et exemples
Dans une étude de cas sur la gestion de la qualité chez Toyota, le système Production System leur a permis de réduire les défauts de production de 50 % en utilisant des méthodes d' analyse des causes racines rigoureusement appliquées, telles que les diagrammes d'Ishikawa (ou diagrammes en arête de poisson) et les 5 pourquoi de Sakichi Toyoda. Malgré une adoption initiale difficile, l'amélioration de la qualité et l'augmentation de la productivité ont rapidement démontré les bénéfices de cette approche.
Les outils d'analyse à utiliser
L'utilisation des bons outils est cruciale pour surmonter ces défis. Par exemple, le diagramme en arête de poisson permet de visualiser et catégoriser les différentes causes potentielles d'un problème. Ces outils sont désormais souvent intégrés dans des logiciels de gestion de la qualité sophistiqués, facilitant ainsi l' analyse des causes racines.
Conclusion
Surmonter ces défis nécessite du temps, des ressources et un engagement ferme envers l'amélioration continue. Une formation adéquate, une communication efficace, et l'utilisation d'outils appropriés peuvent transformer ces obstacles en opportunités pour améliorer la qualité de la production et la performance organisationnelle.
L'importance de l'équipe dans l'analyse des causes racines
Les rôles clés des membres de l'équipe
Chaque membre de l'équipe joue un rôle crucial dans l'analyse des causes racines. Selon Kaoru Ishikawa, père du diagramme d'Ishikawa, l'implication collective garantit une vue complète et diversifiée du problème. Par exemple, dans une étude menée par Toyota, il a été démontré que les solutions trouvées par une équipe hétérogène sont 30 % plus efficaces que celles proposées par des groupes homogènes (Toyota, 2021).
L'importance de la formation et des compétences
Une formation adéquate est essentielle pour une analyse réussie des causes racines. Les membres de l'équipe doivent maîtriser les outils et les méthodes tels que le RCA (Root Cause Analysis). Une étude publiée par l'Acr (Association for Quality and Reliability) en 2022 montre que 85 % des entreprises ayant formé leurs équipes à l'analyse des causes racines ont constaté une amélioration significative de la qualité de leurs produits.
La collaboration et la communication efficace
Pour que l'analyse des causes racines soit fructueuse, la communication ouverte et la collaboration sont cruciales. Sakichi Toyoda, fondateur de Toyota, a souligné que poser les « 5 pourquoi » de manière collective aide à identifier les causes profondes des problèmes. Un rapport de l'entreprise GE en 2020 a révélé qu'une bonne communication au sein de l'équipe a permis de réduire les erreurs de production de 25 % (GE, 2020).
L'intégration de l'analyse des causes racines dans le lean sigma
Integration dans le cadre du Lean Six Sigma
Dans le contexte actuel de l'industrie, il est crucial de maximiser l'efficacité des processus tout en minimisant les gaspillage et erreurs. C'est là que l'analyse des causes racines (RCA) s'intègre parfaitement dans la méthodologie Lean Six Sigma, dont l'objectif principal est l'amélioration continue de la qualité et de la production.
Une étude réalisée par George et Wilson (2004) illustre que les entreprises qui intègrent efficacement l'analyse des causes racines dans leur stratégie Lean Six Sigma enregistrent en moyenne une réduction de 30 % des défauts de production. Ces résultats mettent en lumière l'importance de cette intégration pour optimiser les processus de gestion qualité.
L'utilisation des outils RCA dans le Lean Sigma
L'un des outils les plus prisés pour l'analyse des causes racines est le diagramme d'Ishikawa, ou diagramme en arête de poisson. Cet outil permet une visualisation claire et systématique des causes potentielles d'un problème, facilitant ainsi l'identification des causes racines et la mise en place de solutions efficaces. Par ailleurs, l'approche des 5 Pourquoi, développée par Sakichi Toyoda, s'avère particulièrement complémentaire dans le cadre du Lean Six Sigma pour investiguer les causes cachées des problèmes.
Exemple d'intégration réussie : Toyota
Un exemple emblématique de cette intégration est celui de Toyota. L'entreprise a su combiner l'analyse des causes racines avec la méthodologie Lean Six Sigma, améliorant ainsi ses processus de production et réduisant significativement les défauts. L'utilisation rigoureuse des 5 Pourquoi chez Toyota est citée comme une des clés de leur succès dans leurs pratiques de gestion qualité.
Défis et succès de l'intégration RCA et Lean Sigma
Cependant, l'intégration de ces méthodologies pose certains défis. La résistance au changement, le manque de formation adéquate et la complexité des processus peuvent freiner leur mise en œuvre. Malgré cela, les entreprises qui réussissent à surmonter ces obstacles bénéficient d'une meilleure efficacité opérationnelle et d'une qualité de produit supérieure.
L'intégration harmonieuse de l'analyse des causes racines dans le Lean Six Sigma n'est donc pas seulement bénéfique mais essentielle pour toute entreprise visant l'excellence opérationnelle. Comme le souligne Kaoru Ishikawa : « Une entreprise qui ne fait pas de qualité n'a pas de futur. »
Pour une approche plus détaillée sur l'amélioration continue dans le domaine industriel, n'hésitez pas à consulter cet article complémentaire.
Tendances et innovations dans l'analyse des causes racines
Nouvelles tendances adoptées dans l'industrie
L'industrie continue d'évoluer, et les méthodes d'analyse des causes racines ne font pas exception. Les entreprises cherchent à automatiser et à intégrer cette analyse dans leurs processus pour gagner en efficacité et en précision. Une tendance majeure consiste à utiliser des outils basés sur l'intelligence artificielle pour analyser des volumes de données considérables et identifier rapidement les causes premières des problèmes.Par exemple, Toyota, pionnière des concepts d'amélioration continue, utilise de plus en plus des algorithmes de machine learning pour compléter leurs méthodes traditionnelles d'analyse, comme le célèbre diagramme Ishikawa de Kaoru Ishikawa. Cela permet de croiser les données provenant de différentes sources afin de trouver des corrélations invisibles à l'œil nu humain.
Intégration des outils numériques
L'intégration de logiciels de gestion de la qualité a également modifié le paysage de l'analyse des causes racines. Des outils comme Minitab ou Six Sigma intègrent désormais des fonctionnalités avancées pour faciliter cette analyse. Ces plateformes permettent de standardiser et d'automatiser les processus d'analyse, réduisant ainsi les erreurs humaines et augmentant la réactivité.Approches collaboratives et interfonctionnelles
Les experts soulignent également l'importance de l'approche collaborative dans l'analyse des causes racines. Sakichi Toyoda, créateur de la méthode des 5 Pourquoi, insistait sur la nécessité de faire participer les membres de l'équipe provenant de différents secteurs de l'entreprise, garantissant ainsi une vue d'ensemble du problème. Cette approche interfonctionnelle est désormais facilitée par des plateformes de collaboration en ligne, comme Slack ou Microsoft Teams, permettant une communication et une résolution de problèmes plus fluide.Analyse en temps réel
Grâce à la connectivité des équipements de production (IoT) et à l'analyse en temps réel des données, les entreprises peuvent désormais identifier des problèmes dès qu'ils surviennent. Cette réactivité permet une production sans interruption, réduisant considérablement les pertes et les coûts associés aux temps d'arrêt. Ces technologies permettent également de prévenir les défaillances potentielles en anticipant les pannes à partir des données collectées.Mise en place de formations spécifiques
Avec l'adoption de nouvelles technologies, il est impératif que les équipes soient adéquatement formées à leur utilisation. Des entreprises comme ACR fournissent des programmes de formation spécifique pour maîtriser les outils d'analyse avancés et s'assurer que les principes fondamentaux de l'analyse des causes racines soient respectés. Un bon exemple est Toyota qui propose régulièrement des formations internes sur les meilleures pratiques et les dernières innovations dans le domaine de la gestion de qualité.Ces tendances montrent clairement que l'analyse des causes racines évolue, avec une intégration de plus en plus forte des outils technologiques. Pour en savoir plus sur l'importance de l'assurance qualité dans ces processus, consultez notre article sur l'assurance qualité dans l'industrie pharmaceutique.