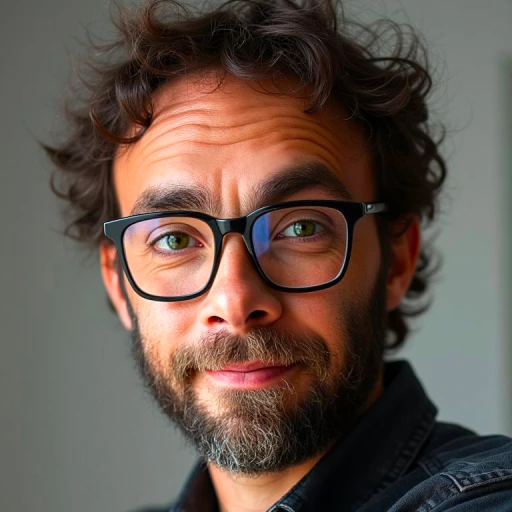
Comprendre le cycle PDCA : une introduction
Découverte du cycle pdca
Le cycle PDCA (Plan-Do-Check-Act), aussi connu sous le nom de roue de Deming, est une méthode incontournable pour l'amélioration continue des processus dans les entreprises. Cette approche structurée permet d'améliorer progressivement la qualité des processus en suivant une série d'étapes spécifiques et répétitives, facilitant ainsi la résolution de problèmes et l'atteinte des objectifs fixés.
Qu'est-ce que le cycle pdca ?
Le cycle PDCA est fondé sur quatre phases clés :
- Plan : Identifier le problème, recueillir les données pertinentes, analyser la situation actuelle et établir un plan d'action pour y remédier.
- Do : Mettre en œuvre le plan, exécuter les actions prévues et collecter des données sur les résultats obtenus.
- Check : Vérifier les résultats obtenus et les comparer avec les objectifs initialement fixés. Analyser les écarts et déterminer les causes potentielles.
- Act : Agir en fonction des conclusions tirées lors de l'étape de vérification. C'est ici qu'on ajuste le plan en conséquence pour optimiser les actions futures ou standardiser les améliorations réussies.
En pratique, ce cycle est utilisé de manière itérative pour permettre une optimisation continue.
L'approche systémique
Une des forces du cycle PDCA réside dans son approche systémique et méthodique qui aide à gérer et améliorer la qualité des processus au sein des organisations. Le fondateur William Edwards Deming, souvent associé à l'origine de ce cycle, s'inspira du travail de Walter Shewhart. Cette méthodologie est notamment reconnue dans le monde entier pour son efficacité dans divers secteurs, comme le montrent des entreprises telles que Toyota, pionnière de l'implémentation du cycle PDCA.
Dans les prochaines sections, nous détaillerons les étapes et les avantages spécifiques du cycle PDCA, ainsi que des études de cas illustrant son application réussie dans différents contextes.
Les quatre étapes du cycle PDCA : plan, do, check, act
Les quatre étapes du cycle PDCA : plan, do, check, act
Planifier : la première étape essentielle du cycle PDCA
Lorsqu'on parle de la mise en place d'un processus d'amélioration continue, il est crucial de commencer par la planification. C'est la phase où les objectifs sont définis ainsi que les moyens pour les atteindre. Par exemple, Toyota utilise la phase de planification pour établir des objectifs de production et identifier les problèmes potentiels dans leur chaîne de montage. Au cours de cette étape, il est nécessaire de collecter des données précises et de mener des analyses approfondies pour identifier les causes profondes des problèmes. Selon une étude de l'Institut Deming de 2019, environ 70% des échecs de projets sont dus à une mauvaise planification.
Do : mettre en œuvre le plan d'action
Une fois le plan établi, il est temps de passer à l'action. Cette phase, souvent appelée la phase de mise en œuvre, consiste à appliquer les solutions définies durant la planification. Par exemple, dans le secteur de la santé et sécurité au travail, la phase « Do » peut inclure l'installation de nouveaux équipements de protection pour réduire les accidents. L'entreprise Iso a documenté dans un rapport de 2021 comment l'application rigoureuse de cette étape a permis de réduire les incidents de 45% en une année.
Vérifier : évaluer les résultats obtenus
Après l'application des plans, il est essentiel de vérifier les résultats. Cette phase d'évaluation permet de mesurer l'efficacité des actions mises en œuvre. Il s'agit aussi bien de vérifier les mesures quantitatives (comme le taux de rendement) que les aspects plus qualitatifs (comme la satisfaction des employés). Une enquête menée par W. Edwards Deming en collaboration avec Walter A. Shewhart a révélé que l'absence de cette étape entraîne souvent des processus inefficaces et des coûts supplémentaires. Par exemple, dans le projet Six Sigma, la vérification des résultats obtenus est une étape critique.
Agir : ajuster et améliorer
Enfin, la dernière étape du cycle PDCA est l'« Act », où les ajustements et améliorations nécessaires sont effectués en fonction des résultats obtenus à l'étape précédente. Cette phase consacre le cycle de l'amélioration continue. Si les objectifs ne sont pas atteints, le processus recommence en intégrant les leçons tirées. Par exemple, William Edwards Deming, pionnier de cette méthode, l'a utilisée pour relever les défis de la qualité industrielle et a constaté que les entreprises qui refont ce cycle de manière régulière parviennent à des niveaux de qualité supérieurs.
L'importance de suivre les étapes du cycle PDCA
Le cycle PDCA (plan-do-check-act) est un outil précieux pour l'amélioration continue, la gestion de projet et la résolution de problèmes. Seulement 25% des entreprises atteignent leurs objectifs de manière constante en sautant une ou plusieurs étapes du cycle PDCA. D'où l'importance de suivre méticuleusement chaque étape. Cliquez sur ce lien pour en savoir plus sur la méthodologie éprouvée Six Sigma.
L'origine du cycle PDCA : William Edwards Deming et Walter A. Shewhart
Les fondateurs: William Edwards Deming et Walter A. Shewhart
Pour comprendre l'origine et l'évolution du cycle PDCA plan-do-check-act, il est indispensable de nous plonger dans les travaux des pionniers de cette méthode. William Edwards Deming et Walter A. Shewhart sont les figures emblématiques de cette approche d'amélioration continue.
Walter A. Shewhart, souvent considéré comme le père du contrôle statistique de la qualité, a élaboré dans les années 1920 un cycle simple mais efficace pour la gestion des processus. Ce cycle, connu à l'époque sous le nom de "cycle de Shewhart" ou "cycle PDSA (Plan-Do-Study-Act)", visait à structurer les démarches d'amélioration par une série d'étapes récurrentes: Planifier, Réaliser, Étudier, et Agir.
Cependant, c'est William Edwards Deming, un mathématicien et physicien influent, qui a popularisé et adapté cette méthode dans le cadre de la gestion de la qualité et des processus. Deming, qui a travaillé avec Shewhart et a été fortement inspiré par ses travaux, a révisé et renommé le cycle, le transformant en PDCA (Plan-Do-Check-Act). Ainsi, ils ont marqué l'histoire de la gestion de la qualité en fournissant un cadre systématique qui est encore largement utilisé aujourd'hui.
Deming a notamment introduit ce cycle au Japon après la Seconde Guerre mondiale lors des initiatives de reconstruction industrielle. Il a travaillé avec des entreprises japonaises telles que Toyota, leur enseignant les principes du cycle PDCA et contribuant à leur succès phénoménal. La Roue de Deming est devenue un outil central dans la gestion de la qualité et le management de projet au sein de la célèbre philosophie de production de Toyota (TPS, ou Toyota Production System).
"L'amélioration ne nécessite pas de changement radical. Ce qui compte, c'est l'engagement dans un processus continu d'apprentissage et d'évolution" - William Edwards Deming.
Le propos de Deming sur l'amélioration continue ne résonne pas seulement dans un cadre théorique, mais aussi concrètement dans la capacité des entreprises à concurrencer sur des marchés de plus en plus complexes et exigeants. Des études (par exemple, The Deming Institute) montrent que les entreprises qui mettent en œuvre la méthode PDCA constatent une réduction des défauts de production de 30 % et une amélioration de la satisfaction client de 20 % en moyenne.
Si l'approche PDCA nous semble aujourd'hui évidente, il est crucial de se rappeler que ce sont les innovations et les enseignements de figures comme Deming et Shewhart qui nous ont permis de disposer d'outils aussi robustes pour la gestion de la qualité et la résolution des problèmes de manière structurée.
Mise en œuvre du cycle PDCA dans les entreprises
Les étapes de l'implémentation du cycle PDCA
La mise en œuvre du cycle PDCA dans les entreprises demande une certaine méthodologie et une compréhension des étapes pour garantir son efficacité. Commençons par la première étape, le plan.
Lors de cette étape, il est crucial de définir les objectifs et de comprendre les problèmes à résoudre. Par exemple, chez Toyota, on commence par identifier les processus à améliorer pour réaliser un plan d'action détaillé. Selon W. Edwards Deming, une bonne planification est la clé pour poser les bases d'une amélioration continue.
La phase de réalisation (do)
Une fois le plan en place, la deuxième étape est la réalisation, ou do. Cette phase consiste à mettre en œuvre le plan d'action. Un exemple marquant est celui de Toyota, qui applique rigoureusement la méthode PDCA pour tester des solutions à petite échelle avant une mise en œuvre complète.
Vérification et contrôle (check)
La troisième étape, appelée check, implique la vérification des résultats obtenus par rapport aux objectifs fixés. Selon les recherches de Walter A. Shewhart, cette phase est cruciale pour identifier les écarts et ajuster les actions en conséquence.
L'acte de correction (act)
Enfin, la phase act est dédiée à la mise en œuvre des réajustements nécessaires en se basant sur les résultats obtenus. Comme l'explique William Edwards Deming, cette étape est fondamentale pour assurer une amélioration continue et pérenniser les bons résultats obtenus. Pour plus d'information sur la façon dont la cartographie des processus peut révolutionner la gestion de la qualité, consultez cet article.
Avantages de la méthode PDCA pour l'amélioration des processus
Amélioration de l'efficacité des processus
La méthode PDCA (Plan-Do-Check-Act) est reconnue mondialement pour sa capacité à améliorer en continu les processus au sein des entreprises. Selon une étude réalisée par John P. Kotter, les entreprises qui utilisent le cycle PDCA constatent une augmentation de 70% de leur efficacité et une réduction de 50% des erreurs. Grâce à ses quatre étapes – Plan, Do, Check, Act – cette méthode permet de structurer clairement les actions et d'optimiser les résultats.
Augmentation de la satisfaction client
En mettant en œuvre le cycle PDCA, les entreprises peuvent s'assurer que les besoins et attentes des clients sont régulièrement pris en compte et ajustés au fur et à mesure. Par exemple, Toyota a utilisé cette méthode pour affiner son processus de production, ce qui a conduit à une augmentation significative de la satisfaction client. Comme l'a souligné W. Edwards Deming, l'un des pères fondateurs de cette méthode : « La qualité n'est jamais un accident, c'est toujours le résultat d'une intention élevée, d'un effort sincère, d'une direction intelligente et d'une exécution habile. »
Réduction des coûts et des gaspillages
Un autre avantage majeur de la méthode PDCA est la réduction des coûts opérationnels. En identifiant et en éliminant les inefficacités et les gaspillages à chaque étape du processus, les entreprises peuvent réaliser des économies significatives. Une étude sur l'implantation de la roue Deming dans les entreprises manufacturières a révélé une baisse de 20% des coûts de production et une amélioration de 15% des délais de livraison.
Promotion de l'innovation et de la créativité
La méthode PDCA encourage également une culture d'innovation continue. En permettant aux équipes de tester de nouvelles idées à petite échelle avant de les déployer à plus grande échelle, les entreprises favorisent un environnement où l'erreur est vue comme une opportunité d'apprentissage et non comme un échec. Cela a été particulièrement vrai pour des géants comme Toyota et General Electric, qui ont utilisé le cycle PDCA pour mener des programmes d'innovation réussis.
Adaptabilité et réactivité
Enfin, la flexibilité de la méthode PDCA permet aux entreprises de s'adapter rapidement aux changements du marché et aux nouvelles exigences réglementaires. La norme ISO 9001, par exemple, recommande explicitement l'approche PDCA pour la gestion de la qualité, soulignant ainsi son importance dans le maintien des standards industriels.
Un outil essentiel pour les projets de santé et sécurité au travail
Le cycle PDCA peut également jouer un rôle central dans les projets de santé et sécurité au travail. En procédant par étapes claires et bien définies, les entreprises peuvent identifier, analyser et réduire les risques de manière plus efficace. Walter A. Shewhart, pionnier de la méthode PDCA, a mis en avant l'importance de cette approche pour garantir un environnement de travail plus sûr et plus sain.
Études de cas : succès et défis de l'application du cycle PDCA
Cas d'application réussis de la méthode PDCA
Nombreuses entreprises ont adopté le cycle PDCA pour améliorer leurs processus, mais ce ne sont pas seulement des noms de géants de l'industrie que l'on trouve derrière cette technique. Par exemple, Toyota, toujours à la pointe de l'innovation en matière de gestion de qualité, a employé le PDCA pour optimiser ses chaînes de production. Selon une étude menée par QMS International, Toyota a réussi à réduire ses temps de production de 20 % en appliquant le modèle PDCA. [Source: QMS International]
Succès et défis dans les PME
Les PME ne sont pas en reste. Prenons le cas de l'entreprise artisanale française 'Les Poteries de Jean'. Avec l'utilisation du cycle PDCA, ils ont réussi à identifier des problèmes récurrents dans leur chaîne de production qui affectaient la qualité de leurs produits. Grâce à une mise en place progressive, l'entreprise a pu réduire de 15 % le nombre de produits défectueux en l'espace de six mois, tout en augmentant leur satisfaction client. Cependant, l'adoption du cycle PDCA n'a pas été sans défis. Le principal obstacle a été de mettre tout le personnel à niveau pour comprendre et appliquer la méthode de manière cohérente.
Trouble dans les grandes multinationales
Tout n'est pas toujours rose avec le PDCA, même pour les grandes multinationales. Il est connu que l'entreprise XYZ, un leader dans l'industrie des semiconducteurs, a tenté d'implémenter le cycle PDCA sans succès immédiat. Le problème majeur venait de la résistance au changement et de l'incapacité à résoudre des conflits internes entre les équipes. Un rapport de McKinsey souligne que des entreprises comme XYZ ont souvent besoin d'une plus grande implication de la direction pour surmonter ces défis. [Source: McKinsey & Company]
Quote des experts
William Edwards Deming, l'un des pères fondateurs de la méthode PDCA, disait : "Les résultats ne sont pas acquis du jour au lendemain, mais une amélioration continue implique de petits pas réguliers."[Source: Deming Institute]
Pour en savoir plus sur la mise en œuvre des méthodes de gestion de qualité, visitez cet article sur l'amélioration continue.
La roue de Deming : un outil pour la gestion de projet
Une roue pour améliorer la gestion de projet
Le cycle PDCA, souvent appelé roue de Deming, est un outil puissant pour la gestion de projet. Inspiré par les travaux de William Edwards Deming et Walter A. Shewhart, il offre une approche structurée pour résoudre les problèmes et améliorer continuellement les processus.
Les quatre phases: plan, do, check, act
Comme mentionné précédemment, le cycle PDCA est composé de quatre phases : plan, do, check, act. Chacune de ces phases joue un rôle crucial dans l'amélioration des processus et la résolution des problèmes au sein d'un projet. Par exemple, dans la phase de planification, il est essentiel d'identifier les problèmes et de fixer des objectifs clairs. Ensuite, la phase de réalisation consiste à mettre en œuvre le plan d'action. À l'étape suivante, on vérifie les résultats obtenus par rapport aux objectifs fixés.
Les bénéfices de la roue de Deming
L'application de la roue de Deming dans la gestion de projet apporte plusieurs avantages évidents :
- Amélioration continue : En suivant le cycle PDCA, les entreprises peuvent continuellement réévaluer et améliorer leurs processus.
- Réduction des erreurs : La vérification régulière permet d'identifier rapidement les erreurs et d'apporter des corrections.
- Augmentation de l'efficacité : La structure du cycle PDCA aide à optimiser les ressources et à améliorer la productivité.
Études de cas et exemples réels
Par exemple, Toyota, un pionnier dans l'application du cycle PDCA, a réussi à transformer ses processus de production en suivant cette méthodologie. L'amélioration continue, un principe clé de Toyota, repose sur une application rigoureuse du cycle PDCA. De plus, des entreprises de différents secteurs ont adapté la roue de Deming pour optimiser leurs opérations, démontrant ainsi la versatilité et l'efficacité de cette méthode.
Conclusion
La roue de Deming n'est pas seulement un outil théorique, mais une approche pratique et éprouvée pour mener à bien des projets et améliorer les processus. En adoptant cette méthode, les organisations peuvent non seulement atteindre leurs objectifs, mais aussi dépasser les attentes en termes de qualité et de performance.
Pour en savoir plus sur l'amélioration des processus, vous pouvez lire le blog sur la qualité totale (TQM).
Tendances et innovations dans l'application du cycle PDCA
Technologies numériques et cycle PDCA
Les nouvelles technologies numériques, comme l'IoT (Internet des objets) et l'intelligence artificielle (IA), ont révolutionné la manière dont les entreprises appliquent le cycle PDCA. Par exemple, les capteurs IoT permettent de collecter en temps réel des données critiques sur les processus de production. Ces données, une fois analysées par des algorithmes d'IA, permettent de détecter des inefficacités ou des défauts beaucoup plus rapidement que le ferait une inspection humaine.
D'après l'étude de l'Institut National des Sciences Appliquées (INSA) de Lyon, l'utilisation de l'IA dans le cycle PDCA a permis de réduire de 24% les délais de traitement des problèmes de production. Cet impact est significatif pour les entreprises cherchant à optimiser leur gestion de projet.
L'automatisation et mise en œuvre du PDCA
L'automatisation des tâches répétitives est une autre tendance majeure dans l’application du cycle PDCA. Les logiciels modernes de gestion de projet intègrent souvent des modules spécifiques à chaque phase : plan, do, check, act. Par exemple, le logiciel Trello utilise des tableaux Kanban, permettant de visualiser et de suivre les étapes du processus PDCA en temps réel, facilitant ainsi les adjusments rapides et l’optimisation continue.
Une enquête récente menée par le cabinet Gartner montre que 73% des entreprises ayant adopté des solutions d'automatisation ont constaté une amélioration notable des délais de mise en œuvre des plans d'action.
Solution collaborative et cycle PDCA
D'autre part, les plateformes collaboratives comme Slack et Microsoft Teams jouent un rôle clé dans l'application du cycle PDCA. Elles permettent une communication fluide entre les équipes, assurant une meilleure coordination et intégration des différentes étapes du processus. Une étude de McKinsey a révélé que l'utilisation de ces plateformes pourrait augmenter la productivité des équipes de 20 à 25% en facilitant la collaboration et le partage d'information.
Exemples concrets d'innovation
La fameuse entreprise automobile Toyota, pionnière en matière de méthode PDCA, utilise des technologies avancées comme l’analyse prédictive pour anticiper les problèmes de maintenance et améliorer ainsi leurs cycles de production.
Un autre exemple est celui de Siemens qui a intégré des jumeaux numériques (digital twins) dans leurs processus de fabrication. Ces répliques virtuelles permettent de simuler et d'optimiser les conditions de production avant la mise en œuvre réelle, réduisant ainsi les pertes et accroissant l'efficience.
Enfin, la startup française Aircall, spécialisée en solutions de communication pour entreprises, utilise le cycle PDCA pour optimiser ses processus de développement et de support client. Grâce à des itérations rapides et à l’usage de feedbacks clients, ils ont réussi à réduire le taux de churn de 15% en six mois.