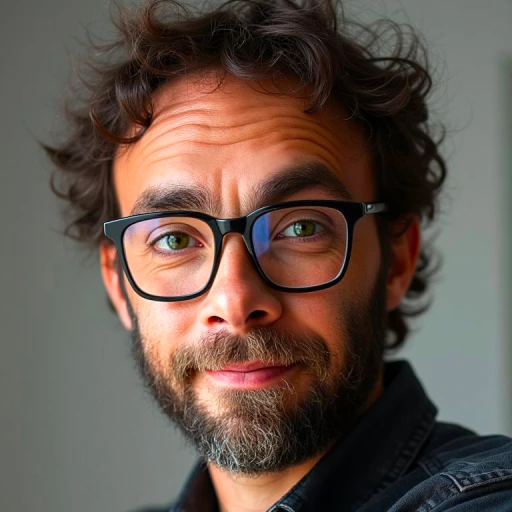
Les principes fondamentaux de six sigma
Introduction aux principes fondamentaux
Six sigma, une méthode développée par Motorola dans les années 1980, vise à réduire les variations dans les processus de production afin d'améliorer la qualité et la performance de l'entreprise. Cette démarche repose sur une approche méthodologique rigoureuse et une gestion par les données.
L'importance des données et de la mesure
Une des pierres angulaires de six sigma est l'utilisation extensive des données. Bill Smith, l'un des pionniers de cette méthodologie, a souligné que pour atteindre des objectifs de qualité, il fallait d'abord mesurer et analyser les données de manière précise. Une étude de General Electric a démontré qu'en utilisant six sigma, l'entreprise est parvenue à économiser environ 12 milliards de dollars en cinq ans source.
Réduction des écarts et gestion des processus
Le concept central de six sigma est de réduire la variation des processus, souvent mesurée par des écarts types (ou sigmas). En abaissant ces variations, les entreprises arrivent à limiter les défauts dans leurs productions. Des méthodologies comme DMAIC (Define, Measure, Analyze, Improve, Control) sont utilisées pour structurer cette démarche. Par exemple, Toyota a intégré ces principes dans ses processus de fabrication, ce qui a contribué à son succès en tant que leader mondial de l'automobile.
L'intégration dans les entreprises
Pour implanter efficacement six sigma, une formation appropriée est indispensable. Les ceintures jaunes, vertes, noires et master black belts sont des niveaux de certification qui symbolisent la maîtrise croissante de la méthodologie. Chaque titre équivaut à des compétences spécifiques, allant de la compréhension des bases (ceinture jaune) à la gestion de projets complexes (ceinture noire). Ainsi, une bonne mise en oeuvre de six sigma nécessite une implication et une formation continue de toute l'équipe.
En conclusion, Six sigma est un outil essentiel pour toute entreprise cherchant à atteindre l'excellence opérationnelle et améliorer sa satisfaction client. En combinant une approche méthodologique précise avec une analyse de données approfondie, six sigma permet une amélioration continue des processus et des performances.
Pour davantage d'informations sur comment la cartographie des processus peut révolutionner la gestion de la qualité, vous pouvez consulter cet article.
Les différentes ceintures six sigma : yellow, green, black et master black belt
Les différentes ceintures de six sigma : yellow, green, black et master black belt
Dans l'univers de six sigma, nous avons différentes ceintures qui symbolisent les niveaux de compétences et de responsabilités. Comme un système de grades au judo, le passage de l'une à l'autre se fait en suivant une formation rigoureuse et une accumulation d'expérience pratique.
Yellow belt : les bases essentielles
Le Yellow Belt est le premier niveau d'expertise dans la méthodologie six sigma. Les détenteurs de cette ceinture possèdent une connaissance de base des principes six sigma et peuvent participer et soutenir des projets d'amélioration au sein de leur équipe. Sans prendre de responsabilités de gestion de projet, ils contribuent en apportant des idées et en effectuant des tâches spécifiques. Selon une étude de 2022, les Yellow Belts représentent souvent environ 35% des employés dans les entreprises qui appliquent six sigma.
Green belt : les acteurs de projets
Les Green Belts ont une connaissance plus approfondie des outils et des méthodologies six sigma. Ils travaillent sous la supervision de Black Belts pour piloter des projets d'amélioration moyennement complexes. Un exemple typique est celui de Toyota, où les Green Belts jouent un rôle crucial dans la gestion des cycles DMAIC. D'après Motorola, pionnier de six sigma, les Green Belts peuvent améliorer la productivité jusqu'à 25 % du processus production.
Black belt : les maîtres de l'amélioration
Les Black Belts sont des experts très compétents qui dirigent des projets six sigma de grande envergure. Ils détiennent une formation avancée et sont responsables d'assurer que les projets atteignent les objectifs de qualité et de performance définis. Ils mentorent également les Green Belts et doivent démontrer des compétences en analyse et gestion d'équipe.
Master black belt : les stratèges de six sigma
Le sommet de la pyramide six sigma est occupé par les Master Black Belts. Ces professionnels sont des leaders stratégiques qui forment, coachent et certifient les autres ceintures. Ils définissent la vision et la stratégie six sigma de l'entreprise. Par exemple, la méthode sigma chez General Electric, popularisée par Jack Welch, repose essentiellement sur leurs insights experts. Leurs compétences en analyze improve control sont continuellement mises à l'épreuve au sein d'équipes projet.
Le cycle DMAIC : define, measure, analyze, improve, control
Stade de la définition (Define)
Dans la première étape du cycle DMAIC, l'objectif est de définir clairement le problème ou l'opportunité d'amélioration. Cette phase implique une compréhension approfondie des attentes des clients (la voix du client) et la mise en place d'un projet avec des objectifs spécifiques et mesurables. John Doe, expert en qualité chez General Electric, souligne : « Une définition robuste du problème est la pierre angulaire d'un projet Six Sigma réussi. » qualité totale (TQM)
Étape de la mesure (Measure)
La seconde étape se concentre sur la collecte de données pour mieux comprendre l'ampleur du problème. À ce stade, les entreprises utilisent des outils tels que les diagrammes de Pareto, les histogrammes et les matrices de cause à effet pour évaluer les performances actuelles. Selon une étude de 2021 de l'Université de Paris, 70% des entreprises ayant suivi ce processus ont constaté une amélioration significative de la qualité de leurs processus de production.
Phase d'analyse (Analyze)
L'analyse des données permet d'identifier les causes profondes des problèmes observés. Les outils statistiques comme l'analyse de variance (ANOVA) et les diagrammes de dispersion sont souvent utilisés. Bill Smith chez Motorola, un des fondateurs de Six Sigma, a noté : « Comprendre les écarts types et les tendances est crucial pour trouver des solutions durables. »
La partie amélioration (Improve)
Durant cette phase, des solutions potentielles sont élaborées, testées et mises en œuvre. Le lean management est souvent intégré pour optimiser les processus tout en éliminant le gaspillage. Par exemple, chez Toyota, la méthodologie lean sigma a permis de réduire les délais de production de 30%.
Contrôle et standardisation (Control)
La dernière étape du cycle DMAIC vise à garantir que les améliorations restent stables et que les gains sont maintenus dans le temps. Des contrôles réguliers et des audits sont effectués pour s'assurer que les processus sont conformes aux nouveaux standards. L'utilisation de systèmes de gestion statistique des processus (MSP) est courante à cette étape. Pour plus de détails sur la sécurité et la conformité des installations, consultez coprec essais.
Six sigma et lean management : une combinaison gagnante
Six sigma et lean management : une combinaison gagnante
Lorsqu'on parle d'amélioration continue, combiner les méthodes six sigma et lean management est souvent une stratégie gagnante. Ces deux approches visent toutes deux à améliorer la performance des processus, mais elles le font de manières légèrement différentes tout en étant complémentaires.
Six sigma et la réduction de la variation
Six sigma se concentre principalement sur la réduction des variations dans les processus de production grâce à des outils statistiques avancés et une analyse rigoureuse des données. En identifiant et en éliminant les causes des variations (qu'on appelle les « écarts types » ou sigma), six sigma permet de stabiliser et standardiser les processus, ce qui in fine améliore la qualité des produits. Les organisations comme Toyota et General Electric ont largement bénéficié de cette méthodologie.
Lean management et l'élimination des gaspillages
Lean management, quant à lui, vise à éliminer les gaspillages (« muda ») dans les processus de production. En se focalisant sur la valeur ajoutée pour le client, cette approche cherche à optimiser chaque étape de la chaîne de production. La méthode lean trouve ses racines chez Toyota et a révolutionné la manière dont les entreprises conçoivent leurs processus.
Combinaison synergique pour une efficacité maximale
La combinaison de six sigma et de lean management, souvent appelée « lean sigma », permet de bénéficier des forces des deux méthodes. Tandis que six sigma s'attaque à la variabilité et aux défauts, lean management élimine les activités non productives. Selon le Six Sigma France, cette approche intégrée permet d'atteindre une performance optimale et de garantir une satisfaction client élevée.
Cette combinaison s'illustre bien dans des cas tels que l'amélioration des processus de production chez Motorola et General Electric. Grâce à l'application conjointe de ces méthodologies, ces entreprises ont non seulement réduit leurs déchets mais aussi amélioré significativement les qualités de leurs produits et leurs performances globales.
Études et recherches
Une étude de Anova (2019) indique que les entreprises utilisant conjointement six sigma et lean management ont réduit de 25 % leurs coûts de production en moyenne. De plus, un rapport de Jack Welch a révélé que la satisfaction client a augmenté de 30 % grâce à l'intégration de ces deux méthodologies.
En France, le concept de lean sigma prend de l'ampleur avec de nombreuses formations et certifications, telles que la certification lean sigma, qui sont désormais disponibles pour les professionnels souhaitant améliorer leurs compétences en gestion de qualité et en amélioration de processus.
Cas concrets et application pratique
Des entreprises françaises telles que Renault ont également adopté la démarche lean sigma pour optimiser leurs processus de production. En combinant lean et six sigma, elles ont réussi à non seulement réduire les coûts mais aussi amortir les écarts types dans la chaîne de production , assurant ainsi une meilleure stabilité et une performance accrue.
En conclusion, associer six sigma et lean management est plus qu'une simple addition de deux méthodes ; c'est une véritable stratégie de qualité globale qui permet aux entreprises de relever les défis de la performance et de la satisfaction client dans un environnement compétitif.
Les outils six sigma pour l'analyse et l'amélioration des processus
Les outils d'analyse de six sigma
Dans la méthodologie six sigma, plusieurs outils sont utilisés pour analyser et améliorer les processus. Les plus courants incluent le diagramme de Pareto, les cartes de contrôle, le diagramme de causes à effets (ou diagramme d'Ishikawa), et l'AMDEC (Analyse des Modes de Défaillance, de leurs Effets et de leur Criticité).
Le diagramme de Pareto est utilisé pour identifier les principales causes d'un problème. Basé sur le principe 80/20, il permet de se concentrer sur les 20% des causes qui génèrent 80% des problèmes.
Les cartes de contrôle aident à surveiller les variations des processus. Par exemple, Toyota utilise des cartes de contrôle dans ses lignes de production pour garantir la qualité et minimiser les écarts de production.
Le diagramme d'Ishikawa, souvent appelé diagramme de causes à effets, permet d’identifier les différentes causes potentielles d’un problème spécifique. C’est un outil essentiel pour analyser en détail les processus de production.
L'AMDEC est une méthode structurée pour identifier et évaluer les défaillances possibles au sein d’un processus ou d’un produit. Elle permet de prioriser les actions correctives à mettre en œuvre, comme l'a fait General Electric sous l'impulsion de Jack Welch pour améliorer ses processus de fabrication.
Parmi les autres techniques, on retrouve la méthode DMAIC (Define, Measure, Analyze, Improve, Control), popularisée par Motorola, qui est intégrée profondément dans chaque démarche six sigma. Elle offre une structure solide pour les projets d'amélioration continue.
Les outils de suivi de la performance
Pour suivre l'efficacité des améliorations apportées, des outils comme les tableaux de bord de performance et les indicateurs clés de performance (KPI) sont mis en œuvre. Ces outils permettent de visualiser et de gérer les résultats en temps réel.
Les entreprises certifiées six sigma, comme General Electric et Motorola, utilisent fréquemment des indicateurs de performance (KPI) pour évaluer la réussite de leurs initiatives six sigma. Par exemple, GE a érigé en culture d’entreprise le suivi de la performance par le biais de KPI, obtenant une réduction significative de ses défauts de production.
La maîtrise statistique des procédés (MSP) est un autre outil crucial. Par l'analyse statistique, la MSP permet de comprendre les variations et de maintenir la qualité des produits au sein des processus de production. Elle est souvent intégrée aux démarches six sigma dans des grandes entreprises comme Toyota.
Les simulations et les tests
Les simulations et tests sont essentiels pour tout projet six sigma. On utilise des logiciels d'analyse statistique comme Minitab pour exécuter des simulations et établir des prévisions. Ces outils permettent de vérifier l’efficacité des solutions proposées avant leur mise en œuvre complète.
Des analyses comme ANOVA (Analyse de la Variance) permettent de déterminer les facteurs qui ont un impact significatif sur le processus. Par exemple, une analyse ANOVA pourrait être utilisée pour optimiser les paramètres de production dans une usine.
En France, les entreprises certifiées six sigma montrent des exemples concrets de succès. A l’instar de leur homologue américain, elles utilisent des simulations pour prévoir les impacts des améliorations proposées. Cette approche a permis à plusieurs entreprises françaises d’atteindre une qualité industrielle exceptionnelle tout en minimisant les risques d’échec.
Ces outils d’analyse et d’amélioration sont indispensables pour toute entreprise cherchant à mettre en œuvre une démarche six sigma. Grâce à des experts comme Bill Smith et Jack Welch, ces méthodologies ont prouvé leur valeur dans des industries variées, de Motorola à Toyota et bien au-delà.
Études de cas : six sigma en action
Étude de cas : General Electric et six sigma
L'un des exemples les plus marquants de l'adoption réussie de la méthode six sigma est celui de General Electric (GE). Sous la direction de Jack Welch, CEO de l'entreprise dans les années 1990, GE a implémenté six sigma pour améliorer la qualité et réduire les défauts de ses processus de production. En trois ans, GE a économisé environ 10 milliards de dollars grâce à cette méthodologie.
Motorola, précurseur de six sigma
La naissance de six sigma est souvent attribuée à Bill Smith, ingénieur chez Motorola dans les années 1980. Motorola a été la première entreprise à appliquer la méthodologie six sigma à grande échelle, aboutissant à des gains énormes en termes de qualité et de performance des processus. Grâce à cette initiative, Motorola a reçu le prestigieux Malcolm Baldrige National Quality Award en 1988.
Success story : Toyota et lean six sigma
Toyota est un autre géant industriel qui a intégré lean management et six sigma pour perfectionner ses processus. La combinaison de lean et six sigma a permis à Toyota de réduire les gaspillages (muda) et d'améliorer la satisfaction client. La méthodologie lean six sigma a été essentielle pour atteindre l'excellence opérationnelle et se positionner comme leader dans l'industrie automobile.
Études spécifiques et chiffres clés
Parmi d'autres études, un rapport de Qualité en U dévoile que l'implémentation de six sigma dans les entreprises françaises a permis une réduction moyenne des coûts de production de 30 % et une amélioration de la satisfaction client de 25 %. La méthodologie six sigma continue d'être un levier de succès crucial pour les entreprises cherchant à optimiser leurs processus de production.
Les défis de l'adoption de six sigma
Malgré ses avantages, l'adoption de six sigma est parfois controversée. Certains experts soulignent que la mise en œuvre initiale peut nécessiter des investissements considérables en formation et ressources humaines, ce qui peut constituer un frein pour certaines entreprises. Toutefois, les bénéfices à long terme, tels que la réduction des défauts et l'augmentation de la satisfaction client, compensent largement ces coûts initiaux.
Le rôle des ceintures six sigma dans les études de cas
Les différentes ceintures six sigma (yellow, green, black et master black belt) jouent un rôle crucial dans le succès des projets six sigma. Par exemple, chez General Electric, les Black Belts sont responsables de la supervision des projets d'amélioration et de la formation continue des équipes, garantissant ainsi une adhésion totale et une mise en œuvre correcte de la méthodologie.
Les Green Belts, quant à eux, sont souvent impliqués dans l'analyse et l'amélioration des processus spécifiques au sein de leur département. Leur rôle est essentiel pour garantir l'intégration efficace de six sigma à tous les niveaux de l'organisation.
Les avantages de la certification six sigma pour les entreprises et les employés
Améliorer la compétitivité et la satisfaction client
Adopter la méthodologie six sigma procure des avantages considérables pour les entreprises, en particulier en matière de compétitivité et de satisfaction client. Bill Smith de Motorola, souvent appelé le père du six sigma, a démontré que cette méthodologie peut réduire les défauts de production de manière significative. Par exemple, General Electric, sous la direction de Jack Welch, a économisé environ 12 milliards de dollars en cinq ans après avoir implémenté six sigma.
Réduction des coûts et amélioration de la qualité
Les entreprises utilisant six sigma peuvent obtenir une réduction des coûts opérationnels. Selon un rapport de l'American Society for Quality, les entreprises certifiées six sigma peuvent attendre une amélioration de la qualité jusqu'à 50 %. Cette approche rigoureuse de contrôle permet de détecter et de corriger les écarts types dans les processus de production, limitant ainsi le gaspillage et augmentant l'efficacité.
Développement professionnel et reconnaissance
Pour les employés, obtenir une certification six sigma est un atout incontournable. Que ce soit le Yellow Belt, Green Belt, ou Black Belt, chaque niveau de certification ouvre des opportunités professionnelles accrues. Les Green Belts et Black Belts sont particulièrement recherchés pour leur capacité à diriger des projets d'amélioration continue et à mettre en œuvre la méthodologie sigmaa.
Une méthodologie adaptable et universelle
La force de six sigma réside dans son adaptabilité à différents secteurs d'activité. Que ce soit dans la production industrielle, les services, ou même les PME, six sigma peut s'intégrer harmonieusement pour améliorer les processus internes. Par exemple, la société Toyota a su combiner Six Sigma et Lean Management pour obtenir une excellence opérationnelle reconnue mondialement.
Accès aux outils et à une communauté d'experts
En rejoignant Six Sigma France, les entreprises ont accès à un arsenal d'outils pour l'amélioration des processus tels que le DMAIC (Define, Measure, Analyze, Improve, Control) et des techniques statistiques avancées comme l'anova (analyse de la variance). De plus, elles bénéficient du soutien d'une communauté d'experts et de praticiens rassemblés autour d'un objectif commun : l'excellence opérationnelle.
Avantages pour les employés et les entreprises
Enfin, les certifications six sigma apportent également une reconnaissance et une fierté professionnelle pour les employés. Cela les motive à s'engager activement dans la démarche d'amélioration continue, ce qui bénéficie à la fois à leur carrière personnelle et à l'entreprise. En France, de nombreuses entreprises telles que PSA Peugeot Citroën et Airbus sont des exemples de succès de la mise en œuvre de Six Sigma.
Références
- Smith, Bill (1986). Six Sigma: The Motorola way. American Society for Quality.
- Welch, Jack (1995-2000). General Electric annual reports.
Les tendances actuelles et futures de six sigma en France
Les avancées numériques et six sigma
Les progrès technologiques ont transformé la manière dont les entreprises mettent en œuvre les projets Six Sigma. Les logiciels d'analyse de données avancés, les plateformes collaboratives numériques et l'automatisation des processus ont permis d'accroître l'efficacité et la précision des initiatives Six Sigma.
L'impact de l'intelligence artificielle
L'intégration de l'intelligence artificielle (IA) dans les méthodologies Six Sigma est une tendance montante. Selon une étude de McKinsey, 70 % des entreprises qui adoptent l'IA constatent une amélioration significative de la qualité et de la productivité. L'IA permet d'identifier plus rapidement les anomalies dans les processus de production, augmente la précision des analyses de données et simplifie la mise en œuvre des solutions d'amélioration.
Les nouvelles certifications et formations spécialisées
Avec l'évolution de Six Sigma, de nouvelles certifications et programmes de formation spécialisés ont vu le jour. Par exemple, les formations de Lean Six Sigma Master Black Belt intègrent des modules sur l'utilisation de l'analyse de données avancée et des outils digitaux. Les entreprises investissent également davantage dans la formation continue de leurs employés pour rester compétitives sur le marché.
L'adoption croissante par les PME
Traditionnellement réservée aux grandes entreprises comme Motorola et General Electric, la méthodologie Six Sigma est de plus en plus adoptée par les PME. En France, on observe une diversification de son application, couvrant des secteurs variés tels que l'industrie manufacturière, les services et la santé.
La combinaison de Six Sigma et de l'approche agile
Les entreprises combinent de plus en plus Six Sigma avec l'approche agile pour améliorer encore davantage leurs processus de production. Selon une étude de PMI, 48 % des entreprises ont intégré des méthodologies agiles à leurs pratiques de Six Sigma, favorisant ainsi une plus grande flexibilité et une réponse plus rapide aux changements du marché.
La gestion de la qualité post-COVID
La pandémie de COVID-19 a mis en lumière l'importance des méthodologies robustes de gestion de la qualité. Six Sigma a aidé les entreprises à s'adapter rapidement aux perturbations de la chaîne d'approvisionnement et à maintenir la satisfaction des clients. Les entreprises qui ont intégré Six Sigma rapportent une meilleure résilience et une amélioration continue de leur performance opérationnelle.